线束多样性随着车辆在电气和电子功能、新通信技术集成、控制和软件应用程序方面的发展而同步增加,成为购买车辆时可用的选项。
这一事实导致了复杂性的增加,并因此增加了线束在车辆重量中所占的重量。例如,在奥迪 A8(2018 版)的情况下,线束重 36 kg,将作为线束一部分的电线放在一起会延伸数公里。梅赛德斯-奔驰 OM654 发动机线束的一个版本提供了一个有用的示例来说明线束的复杂性,其中包含:54 个连接器、116 根电线,拉直后长度覆盖 4 m2,重量为 1.5 kg。
由于线束的复杂性和多样性,线束制造商有两种选择:
- 要么将布线分成更小的模块(如果可能),在每个模块的专用装配线上制造,稍后进行布线的最终组装(在同一生产地点或在汽车制造商附近的地点);
- 或在更大、更复杂的装配线上制造最终布线。但无论他们的选择如何,模块的制造和最终组装都需要相同的制造和组装技术。
生产流程根据实施的装配技术进行组织,通常分为:
- 动态装配线:通常用于制造线束模块和较小的线束。开发了几种类型的动态装配线,但最常见的用于制造不太复杂的线束是由固定的装配板(托盘)组成的,传送带位于线的下部,用于承载线束从一个工段到另一个。生产线的组织方式使用于组装的组件在正面提供,确保工段符合人体工程学。
- 用于大型模块制造和模块最终组装的转盘(也称为转台)。转台由安装在轨道上的几块板组成,因此它可以转动。这种生产技术通常用于将所有工作分解为几个基本任务。装配线由几块板组成,每个操作员在旋转/移动转盘之前执行分配给他的工段的有限数量的操作,这些操作总是相同的。建立生产线的速度可以确保生产率和质量标准。
无论制造商选择使用动态装配线 (LAD) 还是转盘装配线来组装布线,为了提供它,都需要工段和设备来生产作为最终布线一部分的预组装元件。
自动化装配流程对线束制造商来说是一个挑战。自动化线束装配系统必须非常灵活且易于适应,以满足项目各个阶段出现的多样化和动态要求。
自动化线束装配流程的难点:
- 处理困难,因为作为线束一部分的电线是非常灵活的元件并且长度很长;
- 构成最终线束的各种组件:不同长度和直径的电线、端子、密封件、连接器、保护装置、连接件、紧固件等;
- 确保连通性所需的多种操作:简单压接(手动或自动)、双线压接(手动或自动)、超声波焊接、扭绞、将端子线组件穿入连接器、应用保护等;
- 一个项目中生产的线束的多样性,许多参考需要不同的装配板(托盘);
- 项目开发阶段发生的布线架构变更,涉及操作顺序和装配系统的快速修改/调整;
- 售后质量事件带来的变化,虽然比开发阶段小,但也涉及配线系统的快速适配。
线束的设计从电气接线图的实现开始,其中包括所有电气和电子设备,以及它们之间的电气连接。根据他们的操作要求,通过电气研究确定重要的技术方面,例如:
- 确保最佳连接所需的电线直径;
- 保护电线的保险丝的口径(额定值);
- 继电器口径;
- 决定在适当情况下使用绞合线而非单线来消除电磁干扰。
布线结构将考虑由集成在车辆上的区域施加的温度和湿度限制,因此:
- 布线组件必须具有与其运行环境相对应的温度等级;
- 在容易出现高湿度的车辆区域,需要在每根电线上的金属端子压接中使用密封连接器和密封件;
- 电线保护措施的选择将根据线路穿过区域的侵蚀性电位以及装配所施加的灵活性要求进行;
- 为了最佳保护、方向和线路固定,连接将使用零件(电线穿过金属框架时的保护垫圈,用于固定和形成路径的塑料零件等)。
设计过程中一个特别重要的步骤是线束的 3D 建模,这有助于定义如何将线束集成到车辆中。在 3D 模型中,表示了所有组件,这些组件是布线运行环境的一部分。这是建立线束路径的阶段,模拟线束辩论以预测和防止线束与其他部件接触时因线束攻击而导致的未来事件。布线路径必须符合几个条件,例如:
- 通过使用相应的固定元件和线束穿过区域的现有热状态施加的保护,消除与具有侵蚀潜力的元件/区域接近所带来的风险;
- 所选择的路径必须尽可能直接,以免增加不必要的布线长度;
- 路径的选择必须考虑使线束在车辆上的装配尽可能容易的需要。如果确定在车辆上安装布线有困难,则需要修改路径和/或修改线束架构(修改布线漂移的长度,消除或添加固定元件)。
与上述条件的任何偏差都会导致布线发生变化,根据项目的阶段,它会产生更高或更低的成本。
在电气图和 3D 建模的基础上,制作了绘制在接线装配板上的 2D 图。对于转盘式装配线,二维绘图包含线束的完整布局,以及线束装配所必需的指示。每块进入流水线组件的板子上都标有相同的图纸。对于实践中最常用的动态装配线类型,详细阐述了几个二维图,对应于装配过程的特定阶段,在构成装配线的每块板上制作。
- 预装配元件的生产;
- 将线束最终组装所需的预组装元件和其他组件存放在专用空间,通常称为拣选区;
- 在每个生产周期开始时测试有代表性的样品。
为了全面了解当今自动化如何应用于线束生产,本文将详细介绍这些阶段。
剥线皮半自动工段:该类工段由操作员和半自动剥线机组成,用于精度要求特别高的极细同轴电缆。它执行以下操作:全剥、半剥、多步剥、同轴和三轴电缆处理、同轴和三同轴电缆处理(详见下图)。

全自动绞线压接机:这些机器工作精度高,用于对长度较长、截面较小的电线进行特定操作。线束制造商大多使用的自动化绞合压接机具有模块化组成,使其更能适应生产要求。如下图所示,它们可以执行各种任务,例如:线切段、绝缘层去除、密封穿线、压接、扭绞。
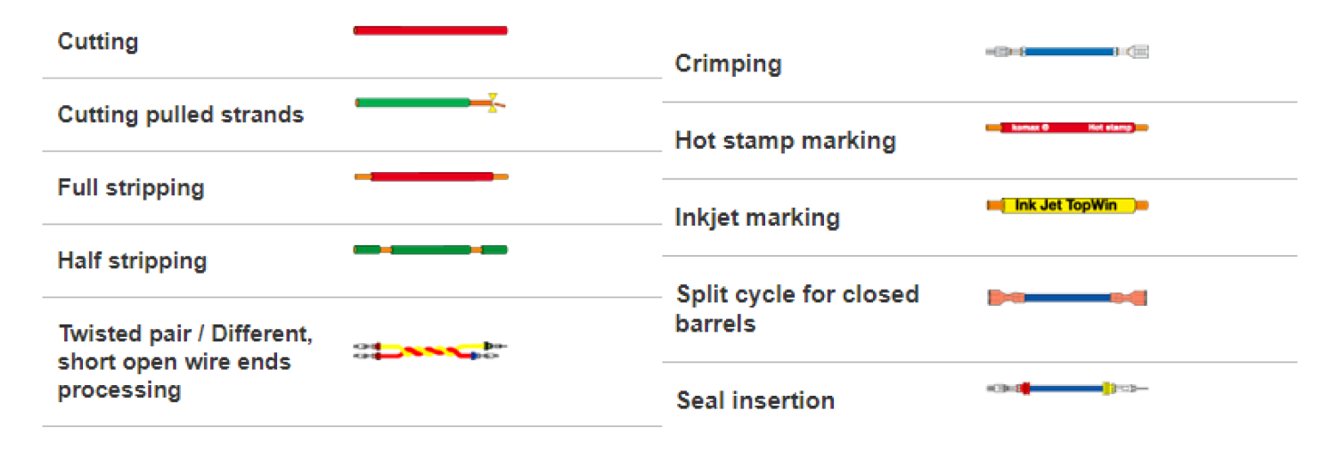
将全自动压接机集成到预装配元件的生产中,显着提高了生产率,同时降低了成本。这些机器能够处理很长的电线长度,用于多种功能,包括双压接(在一个端子上压接两根电线)即使确实存在用于超声波焊接的自动化机器,在实践中进行布线线束需要多种类型的拼接,而这些拼接无法在全自动过程中执行。这是目前超声波焊接仍由操作者使用超声波焊接机实现的主要原因。
热缩管穿入工段:热缩管应用于电线上,通常用于保护接头和压接区域(尤其是在较大横截面的电线上)。这种类型的工段比其他类型的工段简单,要进行的操作非常简单,但必须小心操作,以免损坏设备区域。操作员将管子穿入电线/接头并将其放在热风机顶部,同时旋转组件以均匀分布热量。
测试中心进行的测试类型:
- 拖链测试,
- 扭转作用测试,
- 弯曲测试,
- 燃烧测试,
- 耐介质测试。
在每个生产周期开始时,将对接头(超声波焊接)和压接端子线整体的代表性样品进行耐久性测试和显微质量检查,以确保为半自动和全自动机器设置的参数是一致的符合要求的质量标准。
- 根据印在装配板上的图纸定位电线;
- 将端子穿入连接器;
- 根据组装板上印刷的图纸进行胶带和保护。
每个装配工段由以下部分组成:
- 组装组件的固定组装板,每块板的结构根据其设计的操作而变化;
- 组件存储区的组织方式使得用于组装的组件在前面提供,并由操作员定期提供;
- 位于装配板下方的传送带,用于将线束分支从一个工段传送到另一个工段。
完成组装过程后,将对所有线束进行测试。这是在电气测试和控制表的帮助下完成的,该表专门设计用于对应要测试的线束的架构。由于此测试期间不允许连接连接器,因此测试台配备了特殊装置,可以在不使用连接机构的情况下接触连接器插座中的金属端子。检查接线涉及执行多种类型的测试:
- 电气测试,用于检查接线连续性,
- 气压泄漏测试,以检查必须满足此要求的组件的防水性,
- 通过使用专门为每个连接器设计的装置对杠杆/二次锁定机构进行完整性测试和验证,该连接器具有通过二次闭合确保连接的系统;
- 符合性验证测试根据电气图检查保险丝和继电器的存在。
如果发现错误,在测试结束时系统打印的标签上将指定必须进行润饰。根据缺陷所在的区域,修饰线束可能很困难。例如,要更换单根电线,必须移除整个受影响区域的线束和其他固定元件的保护。
使用专门为此目的创建的工具进行修饰,在不影响其他组件质量的情况下修复缺陷。修图后,恢复所有功能的接线测试过程。
在测试表明接线可以执行所有功能后,打印确认这一事实的标签并将其贴在接线上。包装布线调配也是一个人工过程。完成调配的方式、用于运输的箱子类型以及箱子中存储的电线数量由规格与客户(汽车制造商)共同确定。
图 9 中的图表突出显示了动态装配线的物流流程,概述了手动和自动流程如何在布线生产中结合。
- 13个工段:组装工段10个,测试工段2个,包装工段1个;
- 9个缓冲区:5个缓冲区用于存放元器件,1个缓冲区用于存放测试前的线束,1个缓冲区用于每测试工段存放未通过测试的线束,1个位于包装工段前的缓冲区用于放置包装前的线束;
- 装配板下方安装传送带,确保线束分支从一个工段输送到另一个工段;
- 装配线由19 名操作员提供服务。
模拟了每天8小时,每周5天,即2400 分钟的单班制,如下图所示:

在模拟之后,注意到在工段 4 之后,每个工段的空闲时间逐渐增加,在最后一个工段达到 97.56% 的百分比。
这一事实会影响生产率,导致生产流程堵塞,如下图所示:
为了优化装配流程,考虑了三个假设:
- 第一个假设是通过消除所有工段的空闲时间来减少工作时间,从而解锁生产。在使用修改后的工作时间进行新的模拟后,数据显示此变体无法解决堵塞问题;
- 第二个假设是将“内部允许时间”(生产线供应时间)减半将有助于减少工段的空闲时间;模拟一个班次的装配流程后,没有发现任何改进;
- 第三个假设包括重新分配分配给每个工段的操作并重新评估装配线的工作量。这次消除了堵塞,减少了空闲时间,从而提高了装配线的生产率;根据该假设进行模拟后获得的结果表明,重新分配操作和缩减操作员规模 (OP 13) 可以优化生产流程。
对比优化后与优化前的结果,可以看出优化后流水线的流动性明显提高,生产周期之间的等待时间被消除。
案例研究表明,对于线束装配,由于自动化程度低,影响生产率的主要因素是作业到工位的分布。高负载工段应由经验丰富的操作员(具有高度灵活性)提供服务,并且应战略性地跨线放置,以确保装配流程的流动性并减少等待时间。
在过去的一年中,在寻找线束生产自动化解决方案方面迈出了重要的一步。已经开发出新一代穿线机来应对组件小型化的挑战,但它们在生产流程中的集成取决于灵活性程度以及投资对生产成本的影响。
为了突出线束装配流程自动化的最新趋势,将使用两个自动化机器示例:
第一个示例是一台全自动机器 (Zeta 640/650),它可以执行以下操作:同时切段、剥皮、穿线密封、压接和双压接不同截面和颜色的线材,将生产时间缩短多达 50 %。它还可以制作不同截面和颜色的线束。此类机器的开发表明了寻找自动化设备并将其集成到拣选区的兴趣。
第二个示例是全自动机器 (Omega 745/755),它执行获得电线/连接器子组件所需的所有操作,可以减少在总装线上执行操作的时间和复杂性。根据可用的技术数据,它可以执行以下操作:同时切段、剥皮、密封、穿线和压接多达 36 根不同的电线(无需更换模块),将电线穿入外壳并关闭二次锁连接器外壳。穿入过程由高精度力传感器监控,即使穿入小元件也能确保端子部件正确锁定在外壳中,从而解决元件小型化问题。这些只是用于改进线束生产技术的自动化解决方案的两个示例,还有许多其他仍处于开发阶段的示例,它们肯定会在未来为生产过程增加价值。然而,新开发的技术解决方案的实施将考虑成本问题及其对线束制造商竞争力的影响。
因此,全自动化不会一蹴而就,也不是所有的线束厂商都能做到,但是能够提高自动化程度的厂商,就会比其他厂商有优势,能够生产出更高质量、更好成本的产品。