电路系统的碰撞损伤不仅影响汽车安全相关零件的正常工作,也容易引起电路系统短路或断路造成的电路零件损坏,甚至发生事故。为防止这类事故发生,应在整车研发过程中充分考虑电路系统的碰撞保护。
目前业界对汽车电路系统的碰撞保护研究多集中在油电混合动力或纯电动车辆的高压电路系统上,并且将其分为高压元器件和高压线束进行研究,高压元器件的碰撞损伤评价主要以元器件外壳是否超过其所用材料断裂应变来判断,而高压线束的失效风险评价大多以其是否会受到明显挤压进行主观判定,并无较为明确的量化评价指标。接桂利、朱西产团队用CAE 分析的方法对高压元器件和高压线束进行碰撞评价,其中高压线束采用四面体实体单元建模,以是否被挤压进行风险判断;曾泽江对高压线束采用六面体+四面体实体单元的方式进行了精细化建模,同样采用是否有挤压或剪切风险进行风险判断。这些研究对车辆上大量使用的低压线束并未过多涉及,并且仅是按照碰撞过程中是否有挤压或剪切风险进行定性判定,而这些低压线束不仅在功能上与高压模块及高压线束强相关,而且其失效往往同样会引起较大的安全事故,需要引起足够的重视。
低压线束在整车碰撞工况中的失效情况包括切割和挤压2 类。切割失效主要是零件锐边与线束的点面接触或线面接触导致线束被割破,甚至割断;挤压失效主要是零件沿碰撞方向对线束进行挤压,导致线束绝缘皮破损,金属导线部分露出。切割风险主要通过前期布置设计规避,本文重点研究线束在碰撞挤压时可承受的挤压失效极限,以期获得相应的设计评价指标。
从需要保护的各电路系统中选取最具代表性的几类线束进行挤压失效试验研究,线束横截面积分别为16 mm2、25 mm2、35 mm2,如图1 所示,其余线束评价指标可参考这3 类线束研究结果。
根据接触类型,将挤压形式简化为3种类型,即选择M10螺栓、5 mm钢片、20 mm钢片3种类型的挤压头,分别代表小面积圆面接触、窄面接触和宽面接触,如图2所示。3 种挤压头与3 种线型组合,并同时考虑不同的挤压速度(见表1),组合成如表2 所示的试验矩阵。为减少试验量,根据各参数的相互影响关系,选取表2 中部分组合项进行挤压试验,共计18组试验,其他组合的情况可认为基本能被覆盖。
试验基本过程为,将导线接通数字万用表电阻通断挡,在静态压力机上用选定的挤压头挤压线束,万用表一端接压力机设备,一端接线束内芯金属,万用表发出蜂鸣声时压力机停止加载,终止试验,此时可认为挤压头已接触到线束内部金属导线,线束可判断为被挤压失效。为减小误差,每组试验进行5次,取结果的平均值作为试验结果。图3所示为20 mm钢片挤压试验过程示意。
注:“*”表示选取进行挤压试验的组合项。
3.1 挤压速度对线束挤压变形的影响
25 mm2低压线束挤压试验过程中,主要采集线束变形与线束所受挤压力数据,如图4所示,由图4可知,每种线型在同种挤压头、不同挤压速度下力-位移曲线基本一致,这说明挤压速度对线束的变形量和挤压力影响很小,即在实车碰撞中,同一根线束的变形评价指标不因车辆碰撞速度的不同而有所变化。
3.2 挤压头形式对线束挤压变形的影响
不同挤压头的挤压力-位移曲线如图5所示。分析图5可知,在相同变形量条件下,各种线束均对5 mm钢片的作用反力最小,M10 螺栓次之,20 mm 钢片作用反力最大。这说明,随着挤压接触面积的增加,线束耐受力也增大,在实际碰撞工况中,同一种线束所受周边零件的挤压面积越大,线束被压缩时的变形量也越小。故在前期布置中,应尽可能将线束布置在与周边零件接触面积大的平面区域,即线束的友好界面。

图3 20 mm钢片线束挤压试验示意

图4 不同挤压速度下25 mm2低压线束的力-位移曲线
另外,比较图5a~图5c 可知,25 mm2的线束挤压反力最高,35 mm2的线束挤压反力最小,这说明线束的线径与线束耐挤压力并无直接关系。
3.3 线束挤压变形的评价
统计18 组试验的线束挤压变形量,发现不同截面积的线束变形量差别很大,难以找到较为统一的评价规律,对数据充分研究后,定义变形压缩比为Δ=T/D(其中T 为线束挤压方向上的压缩量,D 为线束挤压方向上的剩余高度),统计线束的变形压缩比如表3 所示,仅有1组数据的变形压缩比为65%,其他组的变形压缩比均集中在70%~80%范围内。因此,可以将线束的变形压缩比作为评价线束挤压失效的判断依据。
分析表3中数据,并综合考虑一定的试验误差及实际碰撞中线束安全保护的工程可行性,将线束失效评价的目标值定义为线束被挤压变形的压缩比≤70%,并可作为车身大多数整车低压线束的碰撞安全设计值。
4.1 CAE建模方法的选择
在整车的正向开发中,为了在项目开发前期较为准确地判断线束的失效风险,除上述失效极限值作为评价指标外,还需要合适的线束CAE 模拟方法。为此,本文结合上述线束试验进行了多种CAE 建模方法的研究。
表3 线束变形压缩比计算结果
低压线束结构见图1b,可考虑采用3 种方法进行CAE 建模简化,如图6 所示:方法1,采用单层六面体单元,线束内芯增加Beam 单元;方法2,采用单层六面体单元,并附增强型橡胶材料属性;方法3,采用双层六面体单元,内层六面体单元附适当强度材料,模拟内芯金属导线,外层六面体单元采用橡胶材料模拟绝缘层,最外层增加壳单元模拟线束护套或定义CAE中与周边零件接触。
随机选择表1 中的组合10、组合14、组合18,即25 mm2线束的试验数据,对上述建模方法分别进行研究,并将研究结果与所有18 组试验结果进行对比,以最终选择具有一定普适性的线束CAE 建模方法。
相关CAE分析结果如图7所示,对25 mm2线束分别进行了M10螺栓、5 mm钢片、20 mm钢片挤压头下的不同建模方法CAE 分析对比,结果表明,采用方法1 时线束的刚度明显较高,而采用方法2 时线束刚度偏低,采用方法3时CAE分析结果与对应试验曲线最为接近,故将方法3的建模方式应用到试验结果对比研究中。
4.2 CAE不同单元尺寸的影响
图8 所示为25 mm2的线束在不同挤压头在单元尺寸2 mm、3 mm、4 mm 下的结果对比。CAE 仿真结果显示,各种压头试验中,4 mm 网格尺寸的结果都与试验结果偏离较远,2 mm 单元的CAE 仿真结果与试验结果拟合度最好,3 mm 单元的CAE 仿真结果也与试验值接近。考虑实际整车碰撞模型的单元数量规模及计算效率,选择3 mm 网格尺寸进行整车线束CAE建模。
4.3 试验数据CAE对比结果
根据上述分析,采用双层六面体3 mm 尺寸的单元进行CAE 仿真与试验结果对比分析,图9 中列出了部分对比结果。其中,每组试验结果均选取了5次试验中同位移条件下挤压力最大、最小值曲线,及5 次试验值的平均曲线,除组合1、组合16和组合22数据偏差较大外,其余仿真曲线与试验结果平均值曲线均较为接近。组合1 的CAE 仿真结果偏高,说明同位移条件下,组合1的线束所能承受挤压力比试验值高,即此模拟中的线束刚度偏高,如用前述试验得到的≤70%的目标值进行前期设计,可能出现CAE分析还未达到目标值,但后期试验验证时已超出目标值的情况,这要求在前期设计时,不只用目标值评价模拟结果,还需结合相应的工程经验,仔细分析仿真结果中线束受挤压情况,给出综合判断;对于组合16,CAE 仿真结果偏低,可认为前期设计进行CAE 分析时如不会出现超标情况,则后期试验验证时,一般也不会出现超出目标值的情况;组合22 中的CAE 仿真结果与试验结果相比,线束刚度前高后低,总体可认为其刚度与试验偏差不大,又因前期CAE 设计分析中主要关心线束何时被挤压失效,而组合22 CAE仿真结果后段刚度偏低,故用≤70%的目标值进行CAE 设计评价时,结果风险可控,当然,为防止有极个别遗漏,仍需结合工程经验仔细分析CAE 结果。综合分析所有对标结果,基本可判断此CAE模拟方法及试验获得的线束评价目标值都可用于线束碰撞保护设计。
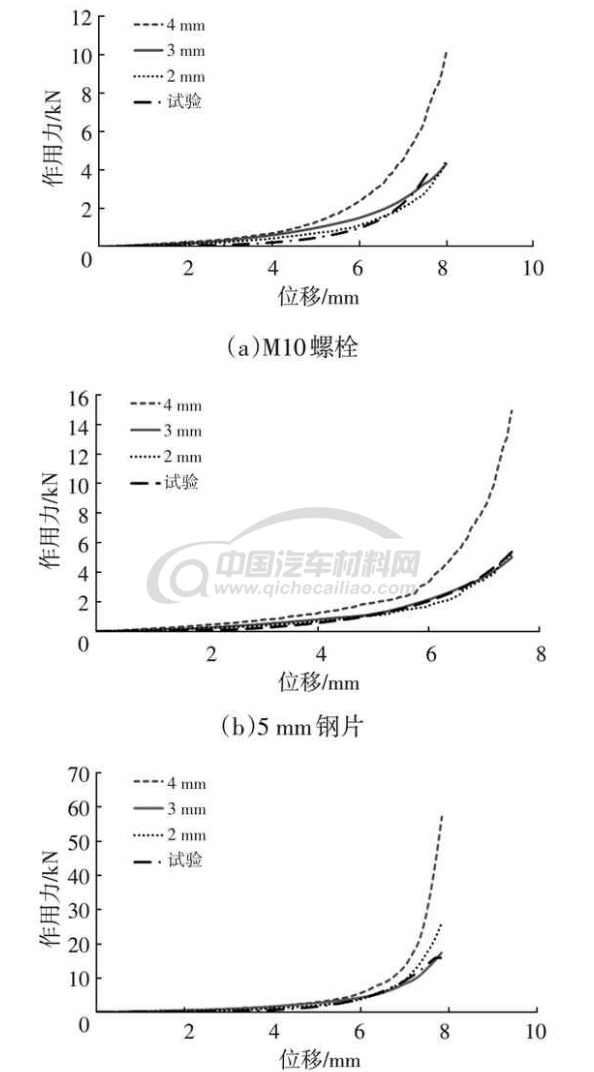
图8 25 mm2线束不同挤压头、不同单元尺寸CAE仿真结果
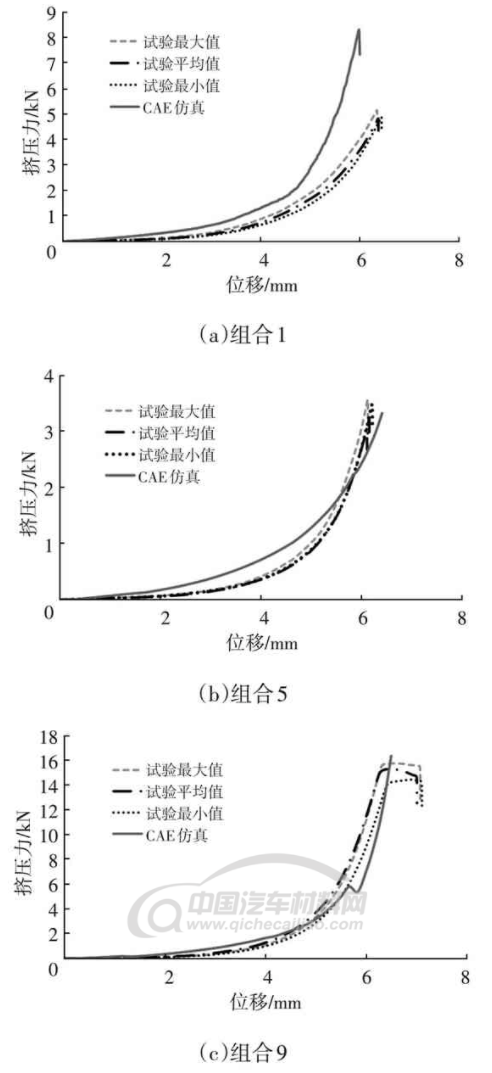
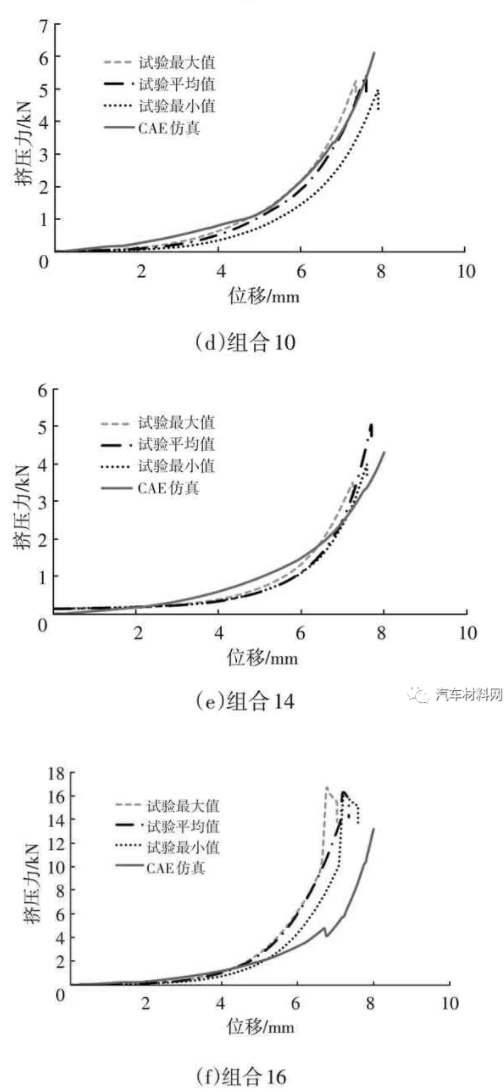
图9 部分组合CAE仿真与试验对比结果
本文从整车碰撞中电路安全性能集成开发的角度出发,对12 V 低压线束在碰撞中的失效评价准则进行研究,得到以下结论:
a.同一线束的破损变形量和周边零件的挤压力不会因为碰撞速度的不同而有所不同;
b.线束在不同挤压头的作用下所受挤压力不同,相同挤压位移条件下,挤压接触面积越大,线束所能承受挤压力也越大,这也表明,线束在布置时如能与周边零件为平面对平面的友好接触,将会大幅降低线束被挤压损伤的风险;
c.线束被挤压破损时的变形压缩比可作为线束碰撞保护的失效评价指标,其目标值可定义为≤70%;
d.推荐选用3 mm尺寸双层六面体单元结构进行CAE建模。
本文研究方法对新能源汽车中的高压线束、冷却管路等各种线路系统的相关保护研究也具有参考意义。